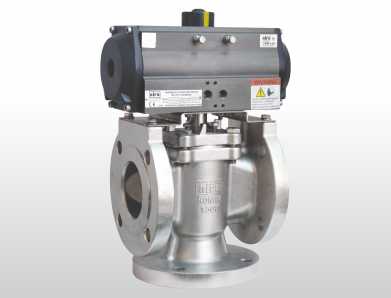
Industrial valves are essential components in various industries, regulating the flow of liquids, gases, or slurries through piping systems. From controlling pressure to managing the flow rate, these devices ensure the efficient and safe operation of industrial processes. Selecting the right valve for a specific application requires a solid understanding of the various types, their functions, and typical uses. This guide provides a detailed overview of the different types of industrial valves, their key functions, and their most common applications, offering insight into how they are integral to multiple sectors.
Types of Industrial Valves
There are several types of industrial valves, each designed to perform specific functions. The most common categories include gate valves, ball valves, butterfly valves, globe valves, check valves, and safety valves. Below is an in-depth look at each type:
1. Gate Valves
Gate valves are primarily used to start or stop the flow of a medium, rather than regulating it. The valve’s mechanism involves raising or lowering a gate (or wedge) inside the valve body to control the flow. They are often employed in applications where the flow needs to be entirely unrestricted or fully blocked, such as in oil and gas pipelines, water treatment plants, and mining.
Key Characteristics:
- Low flow resistance when fully open
- Suitable for high-pressure and high-temperature applications
- Not ideal for throttling purposes
2. Ball Valves
Ball valves are known for their reliable sealing and quick operation. The valve uses a spherical disc (the ball) with a hole in the middle. When the hole is aligned with the flow direction, the medium passes through. When the ball is rotated by 90 degrees, the flow is blocked. Ball valves are popular for applications requiring quick shut-off and minimal leakage.
Key Characteristics:
- Excellent for on/off control without pressure drop
- Suitable for both gases and liquids
- Compact and durable, with a long service life
3. Butterfly Valves
Butterfly valves are widely used for regulating flow in large-diameter pipes. They consist of a rotating disc that opens or closes the flow path. Lightweight, easy to install, and requiring less space than other valve types, these valves are ideal for space-constrained applications.
Key Characteristics:
- Quick to operate (90-degree rotation)
- Suitable for large-volume water applications
- Economical and available in a wide range of sizes
4. Globe Valves
Globe valves are designed primarily for regulating flow. By moving a disc against the flow, they throttle the medium with a linear motion. Due to their throttling capability, globe valves are commonly used in applications where flow regulation is important, such as cooling systems, chemical plants, and oil refineries.
Key Characteristics:
- Excellent flow control
- Higher pressure drop compared to other valves
- Suitable for both on/off and throttling applications
5. Check Valves
Check valves allow flow in one direction and automatically prevent backflow. These valves do not require manual operation, making them ideal for preventing contamination or damage caused by reverse flow. Check valves are commonly found in water and sewage systems, as well as in pump and compressor discharge lines.
Key Characteristics:
- Simple operation (no manual intervention)
- Prevents backflow, protecting equipment
- Available in a variety of designs, such as swing, lift, and ball check valves
6. Safety Valves
Safety valves are essential for protecting systems from excessive pressure. When the pressure in a system exceeds the set limit, the valve opens automatically to release pressure and prevent damage. Safety valves are critical in applications like boilers, pressure vessels, and chemical processing units, where over-pressurization can lead to hazardous conditions.
Key Characteristics:
- Automatically releases pressure when it exceeds safe limits
- Critical for protecting equipment and ensuring safety
- Widely used in high-pressure applications
Functions of Industrial Valves
The primary function of industrial valves is to control the flow of a medium, whether liquid, gas, or slurry, in a piping system. Valves can perform various functions such as starting or stopping flow, regulating flow rate, preventing backflow, and relieving pressure.
Here are the core functions that different valves perform:
- Start and Stop Flow: Gate valves and ball valves are often used for completely stopping or starting the flow of a medium.
- Regulate Flow: Globe valves and butterfly valves are typically used to regulate flow by controlling the rate at which the medium passes through the system.
- Prevent Backflow: Check valves are designed to prevent the reverse flow of a medium, which could cause contamination or damage to other equipment.
- Pressure Relief: Safety valves protect systems from over-pressurization by automatically releasing excess pressure when necessary.
Applications of Industrial Valves
Industrial valves are used across various industries, each of which has specific requirements depending on the medium being controlled and the environmental conditions. Below are some industries where industrial valves play a crucial role:
1. Oil and Gas Industry
In the oil and gas sector, valves are used to manage the flow of crude oil, natural gas, and other petroleum products. The high-pressure and high-temperature environments of this industry demand valves that are durable, reliable, and resistant to corrosion.
2. Water Treatment and Distribution
Valves are essential in water treatment plants and distribution systems. In order to maintain the integrity of the water supply, they control the flow of water, ensure proper pressure levels, and prevent backflow.
3. Chemical and Petrochemical Industries
The chemical industry uses valves to handle a wide range of fluids, including corrosive and hazardous materials. Valves must be designed to withstand harsh conditions, ensuring safe and reliable flow control.
4. Power Generation
Steam flow, cooling water, and boiler pressure are all controlled by valves in power plants. These applications require high-performance valves that can operate under extreme conditions.
5. Food and Beverage Industry
Hygiene is a major concern in the food and beverage sector. Valves used in these industries must be easy to clean and sanitize, often made from stainless steel to prevent contamination.
Conclusion
Industrial valves are indispensable components in countless industries, each serving critical roles in ensuring the efficient and safe operation of processes. With a wide variety of types—each offering specific advantages—understanding the right valve for each application is key to optimizing system performance.
For those looking to invest in industrial valves, selecting reliable valves manufacturers in India is crucial. These manufacturers offer a broad range of valves suited to meet the demands of industries both domestically and globally. As the demand for efficient flow control systems grows, India’s valve manufacturing sector continues to rise to the challenge, supplying durable and high-performance products tailored to the needs of modern industries.