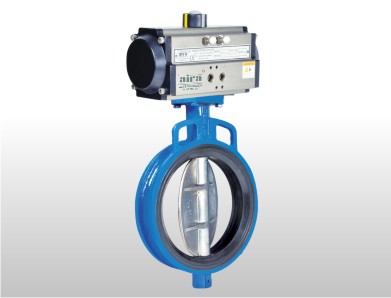
The oil and gas industry is one of the most demanding sectors, requiring high-performance equipment to ensure efficiency, safety, and reliability. Industrial valves play a crucial role in controlling the flow of liquids and gases under extreme conditions. Selecting the right valves is essential to maintaining operational integrity, reducing downtime, and ensuring safety compliance. In this article, we will discuss key considerations when choosing industrial valves in the oil and gas industry, along with insights into how Aira Euro Automation, a trusted valve supplier, meets these critical requirements.
Material Selection
Industrial valves in the oil and gas sector must withstand extreme temperatures, high pressures, and corrosive environments. Choosing the right material ensures longevity and optimal performance. Some common materials include:
- Stainless Steel: Offers high resistance to corrosion and is suitable for offshore applications.
- Carbon Steel: Ideal for high-pressure systems but requires coatings for corrosion resistance.
- Alloy Steels: Provide enhanced durability in extreme conditions.
- Duplex Stainless Steel: Preferred for its strength and corrosion resistance in subsea applications.
Aira Euro Automation manufactures valves using high-quality materials that adhere to industry standards, ensuring durability and efficiency.
Valve Types and Their Applications
Different types of valves are used based on application requirements. Key valve types in the oil and gas industry include:
- Ball Valves: Known for their quick shut-off capabilities, these valves are ideal for high-pressure applications.
- Gate Valves: Used where minimal flow resistance is required, especially in pipeline isolation.
- Globe Valves: Provide precise flow control and are often used in throttling applications.
- Check Valves: Prevent backflow, ensuring the safety and efficiency of pipelines.
- Butterfly Valves: Suitable for large-diameter pipelines with low-pressure drops.
Aira Euro Automation, as a leading valve supplier, offers a wide range of these industrial valves, ensuring their compatibility with diverse oil and gas applications.
Pressure and Temperature Ratings
Valves in the oil and gas industry operate under extreme pressure and temperature conditions. Selecting valves with appropriate pressure and temperature ratings is critical to preventing system failures. Key factors to consider include:
- Pressure Class Ratings: ASME class ratings (150, 300, 600, 900, etc.) indicate the valve's ability to withstand different pressure levels.
- Temperature Range: Valves should be capable of handling both high and sub-zero temperatures to function in extreme environments.
Aira Euro Automation ensures its valves are designed to meet these critical specifications, providing reliable solutions for high-pressure and high-temperature applications.
Compliance with Industry Standards
The oil and gas industry follows stringent regulations to ensure safety and environmental protection. Valves must comply with industry standards, such as:
- API (American Petroleum Institute) Standards
- ISO (International Organization for Standardization) Certifications
- ASME (American Society of Mechanical Engineers) Compliance
- NACE (National Association of Corrosion Engineers) Standards
Aira Euro Automation manufactures valves that meet these global standards, ensuring top-notch quality and regulatory compliance.
Actuation Methods
Depending on operational needs, valves in the oil and gas industry can be operated manually or through automation. Common actuation methods include:
- Manual (Handwheel or Lever) Operation
- Pneumatic Actuators: Ideal for remote operations requiring quick response times.
- Electric Actuators: Used for automated control systems.
- Hydraulic Actuators: Suitable for high-force applications in offshore drilling.
Aira Euro Automation provides various actuation options to suit different operational requirements, enhancing control and efficiency.
Maintenance and Lifecycle Costs
Regular maintenance is essential to ensure the longevity and optimal performance of valves. Key considerations include:
- Ease of Maintenance: Valves should be designed for easy inspection and repairs.
- Availability of Spare Parts: Ensuring quick access to replacement parts minimizes downtime.
- Total Cost of Ownership (TCO): Choosing high-quality valves reduces long-term operational costs.
Aira Euro Automation offers robust and low-maintenance valve solutions, helping industries achieve cost-effective and efficient operations.
Conclusion
Industrial valves are a critical component in the oil and gas industry, impacting efficiency, safety, and operational reliability. Selecting the right valves involves careful consideration of materials, pressure ratings, compliance standards, actuation methods, and maintenance requirements. Aira Euro Automation, a leading valve supplier, provides high-performance valves designed to meet the industry's stringent demands. By choosing the right valves from a trusted manufacturer, oil and gas companies can enhance productivity, ensure safety, and optimize costs.