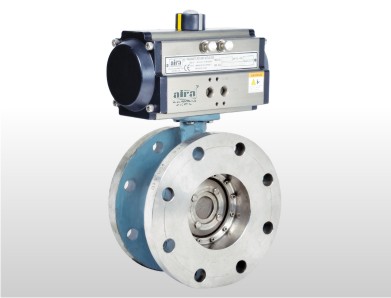
Oil and gas, manufacturing, pharmaceuticals, and water treatment all use industrial valves. These valves regulate the flow of liquids, gases, and slurries, ensuring safe and efficient operations in industrial systems. Choosing the proper valve for a certain application is critical since it influences the system's safety and performance. With numerous types of industrial valves available, including ball valves, gate valves, butterfly valves, globe valves, and check valves, choosing the right one can be challenging. Several factors need to be considered to ensure you select the best valve for your system's requirements.
In this article, we will explore the key factors that should guide your industrial valve selection process.
Application Requirements
The first step in selecting an industrial valve is to understand the specific requirements of your application. Different valves serve different purposes, and each type is designed to handle a specific range of pressures, temperatures, and flow rates. For example:
- Ball valves are ideal for quick shut-off applications and are commonly used in systems requiring tight sealing.
- Gate valves are typically used in systems where full, unobstructed flow is necessary.
- Butterfly valves are suitable for large pipes and applications that involve moderate pressure control.
- Globe valves provide precise flow control and are used in throttling applications.
Knowing the exact purpose of the valve in your system will help narrow down your options and ensure optimal performance.
Material Compatibility
Another critical factor in valve selection is the material compatibility between the valve and the media (fluid or gas) it will control. Valves are made from various materials, including stainless steel, carbon steel, brass, bronze, and plastic. The choice of material will be determined by the media's qualities, such as chemical composition, temperature, and pressure.
- Stainless steel is resistant to corrosion and is suitable for applications involving corrosive chemicals or high temperatures.
- Brass valves are often used for water and non-corrosive fluids due to their affordability and moderate corrosion resistance.
- Plastic valves (like PVC) are lightweight and resistant to chemicals but have limited temperature and pressure tolerance.
Choosing a valve with the right material ensures long-term durability and prevents issues like corrosion or material degradation, which can compromise the system's integrity.
Pressure and Temperature Ratings
Valves are designed to operate within specific pressure and temperature ranges. Selecting a valve with the correct pressure rating (measured in pounds per square inch or PSI) and temperature range is essential for safe and efficient operation. If a valve is exposed to higher pressures or temperatures than it is designed for, it could fail, leading to leakage, system damage, or safety hazards.
Before selecting a valve, assess the operating conditions of your system. Ensure that the valve’s pressure and temperature ratings match or exceed the system’s maximum operating conditions. Valve suppliers typically provide detailed information about the pressure and temperature limits of their products, so make sure to review this information carefully.
Flow Rate and Valve Size
The flow rate and the size of the valve are closely related and must be considered together. Valves come in various sizes, and selecting the wrong size can affect the system's efficiency and performance. If a valve is too small, it will restrict the flow of media, leading to higher pressure drops and reduced efficiency. On the other hand, an oversized valve may cause unnecessary turbulence and cost more without providing any additional benefits.
The flow coefficient (Cv) is an important parameter that indicates how much fluid a valve can pass. Valve suppliers often provide Cv ratings for their products, which can help you determine the appropriate valve size based on the desired flow rate.
Actuation Method
Valves can be operated manually or automatically. Depending on your system’s requirements, you can choose from the following actuation methods:
- Manual valves are operated by hand using levers, wheels, or handles. These are suitable for low-cost, low-complexity systems where automation is not necessary.
- Pneumatic actuators use compressed air to open and close valves automatically. They are common in industrial settings where speed and reliability are critical.
- Electric actuators operate valves using an electric motor, offering precise control over valve position.
- Hydraulic actuators use pressurized fluid to control valve movement and are often used in high-pressure applications.
Selecting the right actuation method ensures optimal control and operational efficiency.
Maintenance Requirements
Maintenance is an essential consideration when selecting industrial valves. Some valves are more maintenance-intensive than others, and regular upkeep may be required to keep them functioning correctly. When evaluating a valve, consider how often it will need maintenance and whether your system can accommodate downtime for repairs or replacements.
For example, ball valves are generally low-maintenance due to their simple design, whereas globe valves with throttling functions may require more frequent checks. Valve suppliers can provide guidance on the expected maintenance requirements for each valve type, helping you choose the one that best suits your operational needs.
Industry Standards and Certifications
Finally, it is crucial to ensure that the valve you choose complies with relevant industry standards and certifications. Compliance guarantees that the valve meets safety, quality, and performance benchmarks, which is especially important in industries such as oil and gas, pharmaceuticals, and food processing.
Look for valves that are certified by organizations such as the American Society of Mechanical Engineers (ASME), the International Organization for Standardization (ISO), or the American Petroleum Institute (API). These certifications indicate that the valve has been tested and approved for use in industrial applications.
Conclusion
Choosing the right industrial valve requires careful consideration of various factors, including application requirements, material compatibility, pressure and temperature ratings, flow rate, valve size, actuation method, and maintenance needs. By understanding these key factors, you can ensure that your selected valve will perform reliably and safely in your system.
It’s also essential to work with a reputable valve supplier who can provide expert advice and guidance throughout the selection process. A knowledgeable supplier will help you evaluate your options, answer technical questions, and recommend the best valve for your specific application. Ultimately, selecting the right industrial valve is an investment in the efficiency, safety, and longevity of your system.