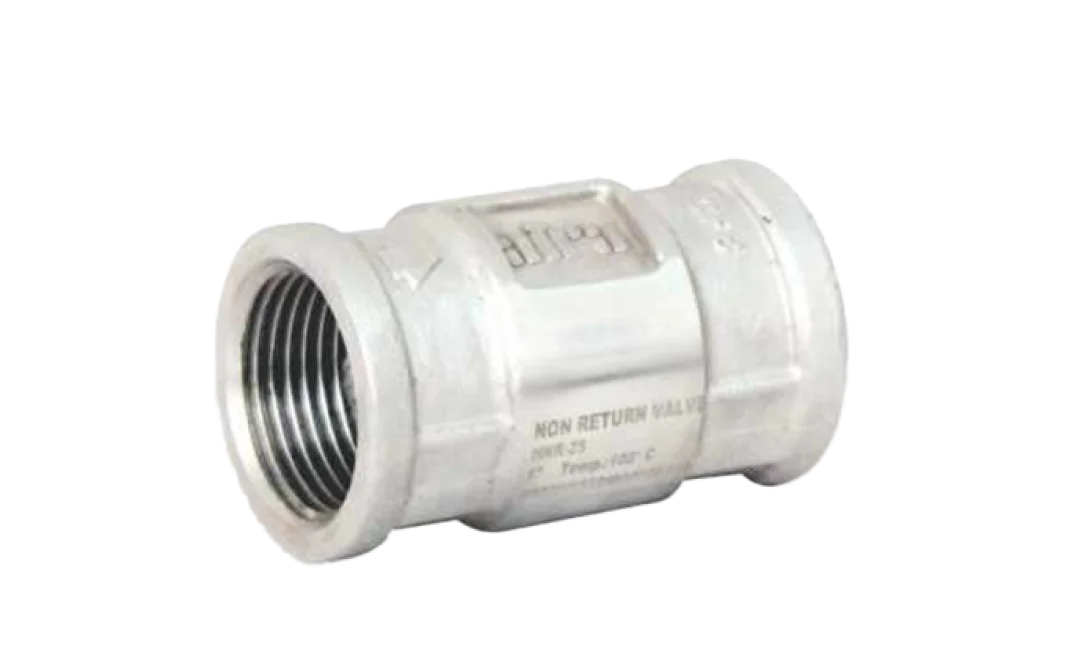
In the world of fluid transportation and pipeline management, ensuring that the flow of liquids and gases moves in the right direction is critical for both safety and operational efficiency. One of the most effective tools used to achieve this goal is the non returning valve—a seemingly simple but essential component in preventing backflow within pipelines. Non returning valves are designed to ensure that fluids or gases move in only one direction, preventing costly and potentially dangerous reverse flow. These valves are crucial to maintaining the integrity of pipelines, protecting equipment, and avoiding contamination.
What is a Non Returning Valve?
A non returning valve, often referred to as a check valve, is a type of valve that allows fluid to flow in only one direction and prevents it from flowing in the opposite direction. Non returning valves are used in a variety of applications, from water supply systems to oil pipelines, and they play a key role in ensuring the integrity and safety of these systems.
These valves operate automatically, meaning they do not require external power sources or manual intervention. When the flow of fluid is in the correct direction, the valve opens, allowing the fluid to pass through. If the flow reverses, the valve closes, effectively sealing the pipe and preventing backflow.
The Backflow in pipelines is a serious concern in many industries. It occurs when the direction of flow is reversed, allowing fluids to flow backward into the system. Backflow can be caused by a variety of factors, including pressure changes, pump failure, or other operational disturbances. The consequences of backflow can be far-reaching and include:
- Contamination of Systems: In drinking water systems, backflow can introduce contaminants into the clean water supply. This poses significant health risks and can violate regulatory standards.
- Damage to Equipment: Many pieces of equipment, such as pumps, compressors, and other system components, are designed to handle flow in one direction. Backflow can damage or destroy these components, leading to costly repairs and downtime.
- Increased Maintenance Costs: Backflow can cause corrosion and wear in pipelines and equipment, leading to frequent maintenance and higher operational costs.
- System Instability: Uncontrolled backflow can cause pressure imbalances in the system, leading to instability, inefficiency, and operational disruptions.
To mitigate these risks, non returning valves are installed at critical points in the pipeline system to ensure that backflow is prevented and that fluid continues to flow in the intended direction.
Types of Non Returning Valves
There are several types of non returning valves, each designed to operate in specific applications. The most common types include:
- Swing Check Valves: These are the most common type of non returning valve. They feature a hinged disc that swings open when fluid flows in the correct direction. When backflow occurs, the disc swings shut, preventing reverse flow. Swing check valves are often used in large pipelines and water distribution systems.
- Lift Check Valves: These valves have a disc or piston that lifts off its seat when fluid flows in the correct direction. When reverse flow is detected, the disc or piston falls back into place to seal the valve. Lift check valves are often used in high-pressure applications.
- Ball Check Valves: Ball check valves use a ball that moves away from the seat when fluid flows in the correct direction. In the event of reverse flow, the ball returns to the seat, blocking the flow. These valves are commonly used in smaller pipelines and low-pressure applications.
- Dual Plate Check Valves: These valves use two plates that open and close in response to the flow direction. Dual plate check valves are typically used in high-pressure systems and are known for their compact design.
Each type of valve has its unique advantages and is chosen based on factors such as the system's size, pressure, and the type of fluid being transported.
How Non Returning Valves Work
The operation of a non returning valve is simple but effective. When fluid flows in the intended direction, it pushes against the valve’s internal mechanism, causing it to open. This allows the fluid to pass through without restriction. If the flow reverses due to pressure changes, pump failure, or other factors, the valve automatically closes, preventing the fluid from flowing backward.
The valve's internal mechanism (which may include a disc, ball, or piston) acts as a barrier to backflow, ensuring that the pipeline system remains intact and that equipment is protected from the damaging effects of reverse flow.
Applications of Non Returning Valves
Non returning
- Water and Wastewater Treatment: Non returning valves are essential in water distribution and treatment systems to prevent contamination. For example, in drinking water systems, a non returning valve prevents treated water from flowing back into the untreated water supply, safeguarding public health.
- Oil and Gas Pipelines: In the oil and gas industry, non returning valves are used to prevent reverse flow that could cause pipeline rupture, equipment failure, or contamination of the oil supply. These valves help maintain the flow of oil, gas, and other fluids under high pressure.
- Chemical Processing: In chemical processing plants, non returning valves are crucial for preventing hazardous chemicals from flowing backward into the system. This is vital for maintaining system integrity and preventing dangerous spills or leaks.
- HVAC Systems: In heating, ventilation, and air conditioning (HVAC) systems, non returning valves help maintain the proper flow of refrigerants and air. They prevent reverse flow, which could disrupt system performance and damage compressors.
- Pumping Stations: Non returning valves are used in pumping stations to ensure that pumps operate in the intended direction, protecting the system from damage and preventing the backflow of liquids or gases.
- Agricultural Irrigation: In irrigation systems, non returning valves prevent the backflow of water, ensuring that each section of the irrigation system receives a consistent and uninterrupted supply of water.
Benefits of Non Returning Valves
Non-ret
- Backflow Prevention: The primary benefit of non returning valves is their ability to prevent backflow, which can cause contamination, damage, and system instability.
- Protection of Equipment: Non returning valves protect pumps, compressors, and other sensitive equipment from reverse flow, helping to extend the life of expensive machinery.
- System Efficiency: By ensuring that fluid flows in the intended direction, non returning valves help optimize the efficiency of pipeline systems, reducing the risk of operational disruptions and downtime.
- Cost Savings: By preventing backflow and the damage it causes, non returning valves help reduce maintenance costs and the need for repairs, leading to long-term cost savings.
- Enhanced Safety: In systems that handle hazardous materials, non returning valves prevent the dangerous backflow of chemicals, gases, or wastewater, ensuring the safety of workers and the environment.
Choosing the Right Non Returning Valve
Selecting the appropriate non returning valve for a particular application requires consideration of several factors:
- Fluid Type: The valve must be compatible with the type of fluid or gas being transported, whether it’s water, oil, chemicals, or air.