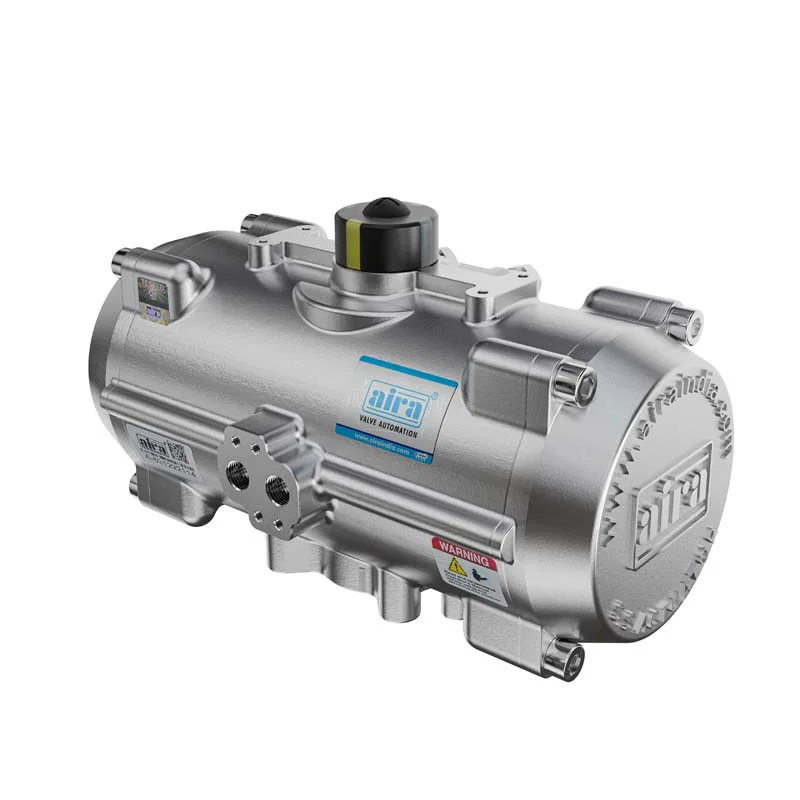
In the world of industrial automation, pneumatic actuators play a crucial role in controlling mechanical motion using compressed air. These devices convert air pressure into mechanical force, enabling precise and efficient movement in various industrial applications. This article explores the different types of pneumatic actuator, their applications, and the benefits they offer.
Types of Pneumatic Actuators
- Linear Pneumatic Actuators These actuators produce motion in a straight line and are commonly used in applications that require pushing, pulling, lifting, or lowering loads. The two main types of linear actuators are:
- Single-Acting Actuators: Operate using air pressure in one direction, with a spring mechanism returning the actuator to its original position.
- Double-Acting Actuators: Use air pressure to move in both directions, offering more control and flexibility.
- Rotary Pneumatic Actuators These actuators convert compressed air energy into rotary motion, making them ideal for applications requiring turning or pivoting movements. There are two common types:
- Rack and Pinion Actuators: Utilize a linear piston motion to rotate a pinion gear, producing rotational movement.
- Vane Actuators: Use a rotating vane inside a chamber to generate torque for rotating components.
Applications of Pneumatic Actuators
Pneumatic actuators are widely used across multiple industries due to their reliability, cost-effectiveness, and efficiency. Some key applications include:
- Manufacturing and Assembly Lines: Used in automated production systems for material handling, sorting, and pressing operations.
- Automotive Industry: Employed in robotic arms, clamping systems, and braking mechanisms for vehicle assembly.
- Aerospace Sector: Utilized in aircraft control systems, landing gear mechanisms, and valve operations.
- Food and Beverage Industry: Essential for packaging, filling, and bottling processes where hygiene and precision are critical.
- Oil and Gas Industry: Deployed in pipeline control valves, regulating the flow of fluids and gases efficiently.
Benefits of Pneumatic Actuators
- High Speed and Efficiency Pneumatic actuators operate at high speeds, making them ideal for applications requiring rapid motion and response times.
- Durability and Reliability With fewer moving parts compared to hydraulic or electric actuators, they have a longer lifespan and require minimal maintenance.
- Cost-Effectiveness They offer a low-cost alternative to other actuator types, as compressed air is readily available and inexpensive.
- Safe and Clean Operation Since they use air as the power source, they are environmentally friendly and suitable for industries requiring contamination-free environments, such as food processing and pharmaceuticals.
- Compact and Lightweight Design Pneumatic actuators are lightweight and compact, making them easy to install and integrate into various systems.
Conclusion
Pneumatic actuators are a vital component of industrial automation, offering speed, reliability, and cost-effectiveness. Their versatility allows them to be used in a wide range of applications, from manufacturing to aerospace. By understanding the different types and benefits of pneumatic actuators, industries can make informed decisions when selecting the right actuator for their specific needs. Whether in automated production lines or precision control systems, these actuators continue to play a pivotal role in enhancing operational efficiency and productivity.