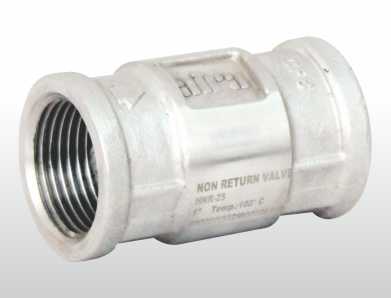
Non return valves, also known as check valves, play a crucial role in various industries by ensuring that fluids flow in only one direction. These valves prevent backflow and protect systems from damage caused by reversed flow. Understanding how non return valves work can help in selecting the right valve for specific applications and ensuring efficient system operation. In this comprehensive overview, we will explore the mechanisms, types, applications, and maintenance of non return valves.
Mechanism of Non Return Valves
Non return valves operate on a simple principle: they allow fluid to flow in one direction while blocking it from flowing backward. This one-way flow is achieved through a combination of mechanical components and pressure differentials.
- Flow Direction: The valve has an internal component, often referred to as the "disc," "flapper," or "ball," which moves in response to the flow of fluid. When fluid flows in the designated direction, the internal component moves away from the valve seat, allowing the fluid to pass through. When the flow reverses or stops, the component returns to its seated position, effectively blocking any reverse flow.
- Pressure Differential: The operation of non return valves relies on the pressure differential between the inlet and outlet. When the pressure at the inlet is higher than at the outlet, the valve opens. Conversely, if the pressure at the outlet exceeds the inlet pressure, the valve closes, preventing backflow.
Types of Non Return Valves
There are several types of non return valves, each designed for specific applications and operational conditions. The most common types include:
- Swing Check Valve: This type features a disc that swings on a hinge or pivot. When fluid flows through the valve, the disc swings open. If the flow reverses, the disc swings back to its seat, blocking the reverse flow. Swing check valves are suitable for low-velocity applications and are often used in water and wastewater systems.
- Lift Check Valve: In lift check valves, the internal disc or ball lifts off the seat to allow flow. When the flow stops or reverses, the disc or ball returns to its seat under the force of gravity or a spring mechanism. Lift check valves are commonly used in high-pressure applications and are effective in preventing water hammer.
- Ball Check Valve: This valve uses a ball that moves up and down within the valve body. When fluid flows in the correct direction, the ball is lifted off its seat. If the flow direction reverses, the ball returns to the seat, blocking backflow. Ball check valves are suitable for applications involving slurries or fluids with solid particles.
- Double Check Valve: A double check valve consists of two check valves installed in series. This configuration provides an additional layer of protection against backflow and is commonly used in water systems to prevent contamination.
- Tilting Disc Check Valve: This valve features a disc that tilts on a hinge. The tilting action allows for a smoother flow and reduces pressure loss. Tilting disc check valves are often used in high-flow applications and are effective in preventing water hammer.
Applications of Non Return Valves
Non return valves are widely used across various industries, including:
- Water and Wastewater Systems: In municipal water systems, non return valves prevent backflow and protect pumps and other equipment from damage. They are also used in wastewater systems to prevent the backflow of contaminated water.
- Oil and Gas Industry: Non return valves are critical in the oil and gas industry to prevent backflow and protect pipelines and equipment from damage. They are used in both upstream and downstream operations.
- HVAC Systems: In heating, ventilation, and air conditioning (HVAC) systems, non return valves prevent the backflow of air and water, ensuring efficient system operation.
- Chemical Processing: Non return valves are used in chemical processing to prevent the backflow of corrosive or hazardous chemicals, protecting equipment and ensuring safety.
- Food and Beverage Industry: Non return valves are employed in the food and beverage industry to prevent contamination and ensure the hygienic handling of products.
Maintenance and Troubleshooting
Proper maintenance of non return valves is essential to ensure their reliable operation and longevity. Key maintenance practices include:
- Regular Inspection: Periodically inspect non return valves for signs of wear, corrosion, or damage. Check for any leaks or unusual noises during operation.
- Cleaning: Depending on the application, non return valves may require cleaning to remove debris or buildup that could affect their performance.
- Testing: Test the valve periodically to ensure it opens and closes correctly. Verify that it effectively blocks reverse flow.
- Replacement: Replace damaged or worn-out non return valves promptly to prevent system failures or contamination.
Conclusion
A non return valve is vital components in fluid systems, providing protection against backflow and ensuring the smooth operation of various industrial processes. By understanding their mechanisms, types, and applications, you can select the appropriate valve for your needs and maintain it effectively. Whether in water systems, oil and gas operations, or chemical processing, non return valves play a crucial role in safeguarding equipment and ensuring system efficiency.