Pneumatic cylinders offer numerous advantages, making them a preferred choice across various industries. Here are some key benefits:
Efficiency:
- Pneumatic cylinders operate at high speeds, enhancing productivity in manufacturing processes.
- They provide precise control over movement, allowing for accurate positioning of components.
- Quick response times enable rapid cycling, minimizing downtime and maximizing output.
Reliability:
- Pneumatic systems are robust and durable, with minimal maintenance requirements.
- They are resistant to harsh environments, ensuring consistent performance even in challenging conditions.
- Simple design and fewer moving parts contribute to reliable operation and longevity.
When considering pneumatic solutions, it's essential to partner with a trusted manufacturer. As the top pneumatic cylinder manufacturer in India, Airmax Pneumatic ensures quality, performance, and reliability in every product.
Cost-effectiveness of Pneumatic Systems in Industrial Settings
In the realm of industrial operations, efficiency is paramount. Pneumatic systems stand out as a cost-effective solution, offering a myriad of benefits that contribute to streamlined processes and reduced expenditure. Here's why they are a top choice:
- Low Initial Investment: Pneumatic systems typically require lower upfront costs compared to their hydraulic or electric counterparts, making them accessible for businesses of varying scales.
- Energy Efficiency: Pneumatic systems boast high energy efficiency, consuming minimal power during operation and lowering utility bills.
- Minimal Maintenance Requirements: With fewer moving parts and simple designs, pneumatic systems demand less maintenance, translating to lower servicing costs and reduced downtime.
- Versatility: Pneumatic systems can be easily integrated into diverse industrial applications, offering flexibility and adaptability to changing production needs.
- Longevity: Well-maintained pneumatic systems have a long operational lifespan, ensuring prolonged usage without significant replacement costs.
For businesses seeking a reliable and efficient solution, investing in pneumatic systems proves to be a prudent choice, supported by their cost-effectiveness and performance. When it comes to pneumatic equipment, choosing the right provider is crucial. As the top pneumatic cylinder manufacturer in India, delivers quality products tailored to meet industrial demands, ensuring optimal performance and cost efficiency.
Flexibility and Versatility: Adapting Pneumatic Cylinders to Diverse Applications
In today's industrial landscape, pneumatic cylinders stand out as versatile workhorses, offering adaptability across a wide range of applications. Here's how:
- Modularity: Pneumatic cylinders come in various sizes, shapes, and configurations, allowing for easy integration into diverse systems.
- Adjustable Force: With adjustable pressure and stroke lengths, these cylinders cater to different operational requirements, offering precise control and efficiency.
- Environmental Adaptability: Pneumatic cylinders excel in harsh environments, resisting dust, moisture, and temperature extremes.
- Cost-Effectiveness: Compared to hydraulic or electric alternatives, pneumatic cylinders often offer a more economical solution without compromising performance.
- Ease of Maintenance: Simple designs and fewer moving parts make maintenance straightforward, reducing downtime and operational costs.
As the Top Pneumatic Cylinder Manufacturer in India, we understand the importance of flexibility and versatility in industrial applications. Our products are engineered to meet the diverse needs of our customers, ensuring reliability and efficiency across various sectors.
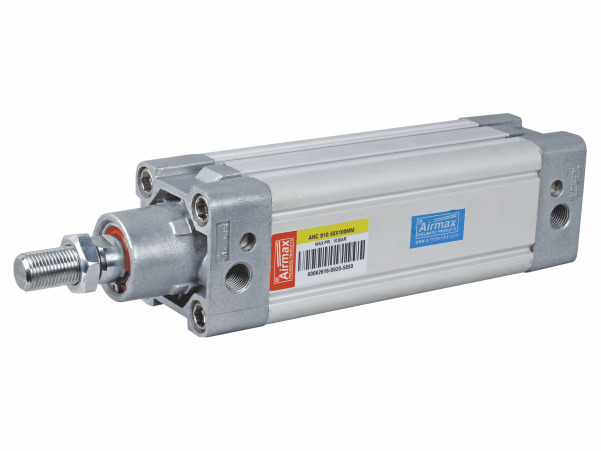
Rapid Response Time: Enhancing Productivity with Pneumatics
In today's fast-paced industrial landscape, maximizing productivity hinges on swift response times. Pneumatic systems emerge as indispensable allies, ensuring efficiency and agility in diverse applications. Here's how:
- Instantaneous Actuation: Pneumatic systems boast rapid response times, facilitating swift actuation of cylinders and valves.
- Minimal Downtime: With quick response capabilities, pneumatic setups minimize downtime, ensuring continuous operation and higher output.
- Precise Control: Pneumatics offer precise control over motion and force, optimizing processes and enhancing product quality.
- Adaptability: Pneumatic systems are versatile, suitable for a wide array of industries and applications, from manufacturing to automotive assembly lines.
- Cost-Effective Solutions: Leveraging pneumatic technology translates to cost-effective solutions, optimizing resource utilization and driving profitability.
Unlocking the potential of pneumatics for enhanced productivity is paramount. Partnering with the Top Pneumatic Cylinder Manufacturer in India ensures access to high-quality components and expert support, propelling your operations towards peak efficiency and competitiveness.
Clean and Environmentally Friendly Operation of Pneumatic Systems
Clean and environmentally friendly operation of pneumatic systems is crucial for sustainable industrial practices. Here's how:
- Efficient Energy Usage: Pneumatic systems consume less energy compared to hydraulic systems, reducing overall energy consumption.
- Minimal Fluid Usage: Unlike hydraulic systems, pneumatic systems utilize air as the working fluid, minimizing the risk of fluid leakage and contamination.
- Reduced Emissions: Pneumatic systems produce fewer emissions since they primarily use compressed air, contributing to a cleaner environment.
- Proper Maintenance: Regular maintenance of pneumatic systems ensures optimal performance, reducing the likelihood of leaks and energy wastage.
- Recyclable Components: Many pneumatic system components are recyclable, promoting a circular economy and reducing environmental impact.
- Compliance with Regulations: Adhering to environmental regulations ensures responsible operation and mitigates any adverse effects on the environment.
For businesses seeking eco-friendly solutions, partnering with the Top Pneumatic Cylinder Manufacturer in India can ensure sustainable practices throughout their operations.
Limitations of Pneumatic Cylinders: Pressure and Force Considerations
Pressure Limitations:
- Pneumatic cylinders operate within certain pressure ranges, limiting their force output.
- High-pressure requirements may necessitate larger, more expensive components.
- Excessive pressure can lead to cylinder failure or leakage, impacting performance and safety.
Force Considerations:
- Pneumatic cylinders exert force proportional to the air pressure and piston area.
- Limited force output compared to hydraulic or electric actuators, especially in high-force applications.
- Inconsistent force output at varying pressures, affecting precision and control in critical operations.
Impact on Applications:
- Limitations in pressure and force may restrict the suitability of pneumatic cylinders for heavy-duty tasks.
- Precision applications requiring consistent force may necessitate alternative actuation methods.
- Manufacturers and users must carefully assess pressure and force requirements to select appropriate cylinder types.
Considering these factors, even the top pneumatic cylinder manufacturer in India faces challenges in meeting the diverse needs of industrial applications.
Temperature Sensitivity: Challenges in Extreme Environmental Conditions
In industries like manufacturing and aerospace, temperature sensitivity poses significant hurdles. Here's a glimpse into the complexities and solutions:
- Material Integrity: Extreme temperatures can compromise material integrity, affecting performance and longevity.
- Thermal Expansion: Differential thermal expansion in components can lead to misalignments or failures.
- Fluid Behavior: Temperature fluctuations alter fluid properties, impacting hydraulic and pneumatic systems.
- Instrument Calibration: Precision instruments require meticulous calibration to maintain accuracy in varying temperatures.
- Heat Dissipation: Efficient heat dissipation mechanisms are crucial to prevent overheating in sensitive equipment.
Navigating these challenges demands innovative solutions and robust engineering. From advanced materials to thermal management systems, every aspect requires meticulous attention to detail. For instance, the top pneumatic cylinder manufacturer in India integrates temperature-resistant materials and precision engineering to ensure reliability in extreme conditions. Adapting to temperature sensitivity is not merely a challenge; it's an opportunity for advancement and excellence.
Maintenance Requirements and Downtime Considerations
Schedule routine checks to detect potential issues early on and prevent unexpected downtime.
- Lubrication: Ensure proper lubrication of pneumatic cylinder components to maintain smooth operation and extend their lifespan.
- Component Replacement: Replace worn-out or damaged parts promptly to prevent further damage and minimize downtime.
- Cleaning: Keep pneumatic cylinders and associated equipment clean to prevent contamination and ensure optimal performance.
- Training: Provide adequate training to maintenance staff to perform inspections, lubrication, and minor repairs effectively.
- Emergency Response Plan: Develop a comprehensive plan to address unexpected downtime, including quick access to spare parts and skilled technicians.
When considering maintenance requirements and downtime, partnering with the top pneumatic cylinder manufacturer in India can ensure reliable performance and efficient support for your industrial operations.