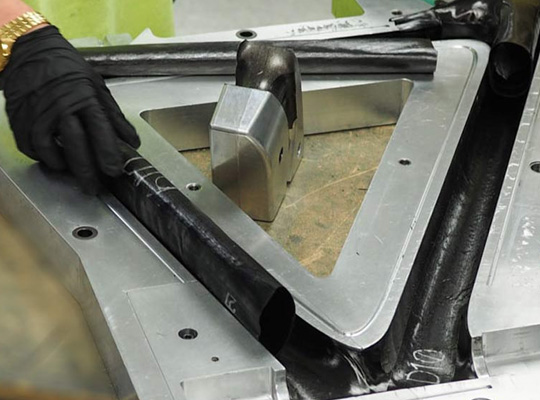
Carbon fiber composites are exceptional materials that are stepping into every industry. They have revolutionized industries and daily use products with their incredible weight to strength ratio, corrosion-resistance and many positive characteristics. Carbon fiber is ideal for many applications such as aerospace, automotive, orthopedic, medical and industrial applications. The world of carbon fiber composites has a diverse range of manufacturing techniques. Each manufacturing method is tailored to meet the demands of the specific carbon fiber products. The manufacturing process is different for sheets compared to rods, tubes, and CNC parts. Bladder molding is a manufacturing technology to create hollow carbon fiber shapes and designs. To help you understand better, in this blog we’ll discuss the process of bladder molding, application with carbon fiber, and its impact on various industries.
What is Bladder Molding?
The carbon fibre composite manufacturing process of bladder molding is used for complex hollow shapes. The technology utilizes an inflatable bladder and a mold. The carbon fiber composite material is placed inside the mold cavity. With the help of pressure, the composite material is spread on the inner surface of the mold. With heat application the composite is solidified. After the curing process (solidifying), the finished carbon fiber product is removed from the cavity.
Steps of Bladder Molding Manufacturing Process
1st Step - Mold Preparation
A female mold replicating the desired final shape is prepared.
2nd Step - Bladder Selection
Select the bladder. Made from heat-resistant materials like silicone or rubber, it closely resembles the inner geometry of the part being formed.
3rd Step - Layup of Composite Material
In this step, you layup the composite material with sheets of fibers impregnated with a special resin, also known as “pre-preg.” Once we have the pre-preg carbon fiber sheets, they wrap them around an inflatable bladder. The chosen composite material is meticulously layered onto or around the bladder.
4th Step - Mold Closure and Bladder Inflation
Once the composite material is positioned, the mold is securely closed. The bladder is then inflated with compressed air, exerting pressure on the composite layers. This pressure ensures that the composite material is optimally spread inside the mold cavity eliminating air pockets or voids.
5th Step – Curing
With the mold sealed and the bladder inflated, heat and pressure or either of one is applied to initiate the curing process. The resin within the prepreg solidifies, permanently bonding the carbon fibers and forming the final composite part.
6th Step - Demolding and Finishing
After curing is complete, the mold is carefully opened, and the now-rigid composite component is removed. The bladder is deflated and retrieved. Depending on the application, the part may undergo additional finishing touches, such as trimming, sanding, or painting.
Industries that work with Bladder-Molded Carbon Fiber Composites
The advantages of bladder molding with carbon fiber are used in various application across industries.
Aerospace: Bladder-molded carbon fiber components find use in aircraft fuselages, wings, control surfaces, and interior components, contributing to improved fuel efficiency and overall aircraft performance.
Automotive: Bladder-molded carbon fiber is used in the design of body panels, hoods, and structural elements offer significant weight savings, leading to enhanced performance and fuel economy.
Marine: From high-performance racing yachts to luxury sailboats, bladder-molded carbon fiber components contribute to superior strength-to-weight ratios, resulting in faster and more maneuverable vessels.
Sporting Goods: Bicycles, kayaks, and even high-end fishing rods benefit from the lightweight strength of bladder-molded carbon fiber components, enhancing performance and user experience.
Medical Devices: The medical field finds applications for bladder-molded carbon fiber in prosthetics and orthotics, where strength, weight reduction, and biocompatibility are crucial factors.
The manufacturing process of bladder molding isn't a one-size-fits-all process. Beyond the standard inflatable bladder, variations exist like expandable bladders that fill the mold cavity as they inflate, conforming to complex shapes. In some cases, vacuum bagging can be employed alongside bladder molding to further remove air pockets and improve laminate consolidation.
NitPro Composites are reputed manufactures of carbon fiber composites products. Specialized in latest technologies carbon fiber products are adopted in a wide range of industries. Explore endless potential in aerospace, automotives, medical industry, orthopedic parts, telescopic poles and so much more. Check out high-strength, light-weight and corrosion-resistant rods, tubes, sheets, CNC parts, fabric and customized designs.
Source by- https://www.atoallinks.com/2024/what-is-bladder-molding/