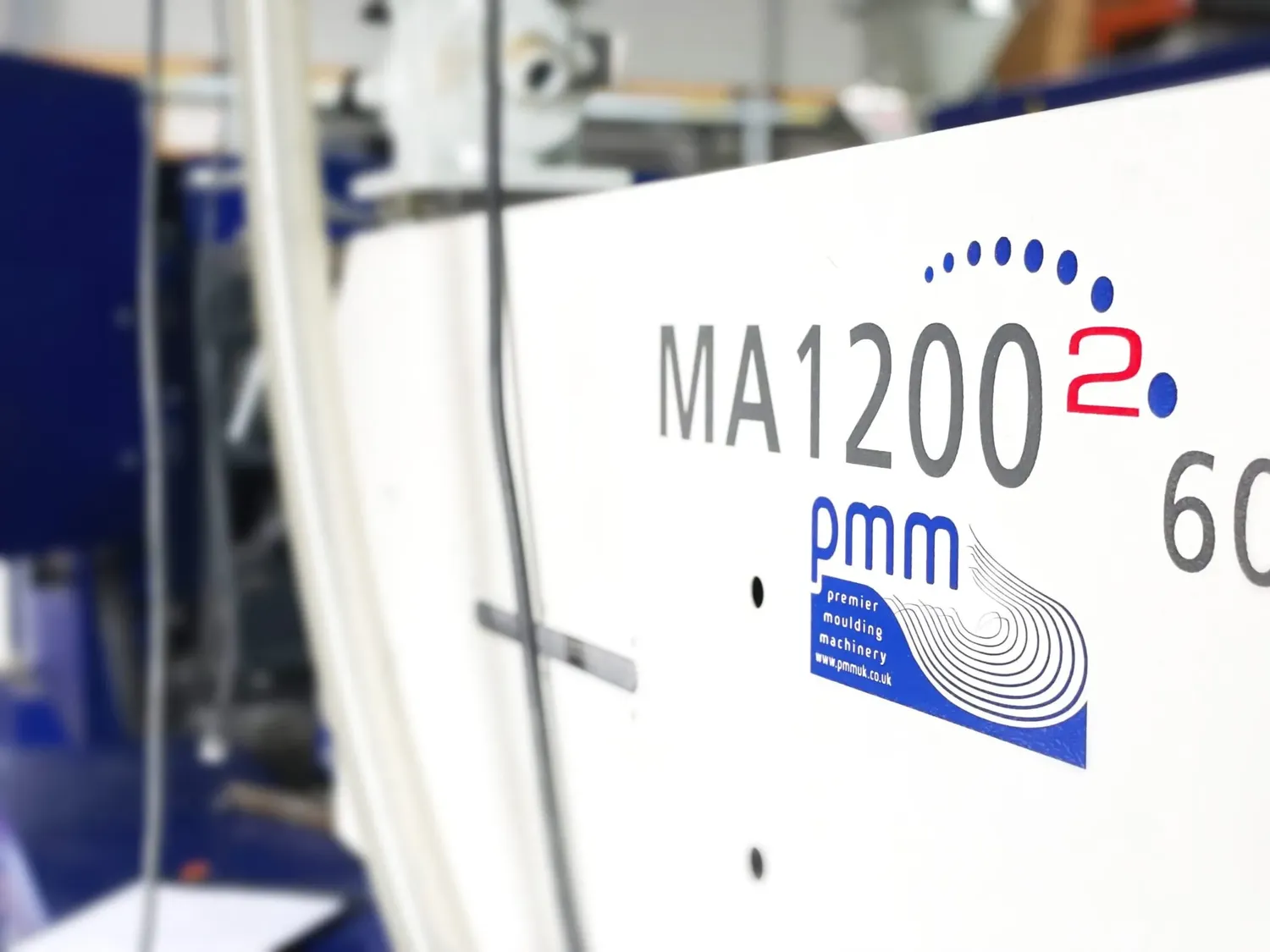
When it comes to manufacturing plastic components, injection moulding stands out as one of the most effective and widely used techniques.
However, within this realm, there are various approaches, two of the most prominent being precision injection moulding and traditional injection moulding. Understanding the differences between these two methods is crucial for manufacturers, product designers, and business owners who want to select the right process for their specific needs.
In this article, we'll delve into the key distinctions, benefits, and applications of precision injection moulding compared to traditional injection moulding.
Understanding Injection Moulding
Before diving into the nuances of precision injection moulding and traditional injection moulding, let's first establish what injection moulding is.
This manufacturing process involves injecting molten plastic into a pre-designed mould, where it cools and solidifies to form the desired shape. It is highly valued for its ability to produce high volumes of complex parts with consistent quality, making it a go-to choice across industries such as automotive, healthcare, consumer goods, and electronics.
Traditional Injection Moulding: An Overview
Traditional injection moulding typically involves using standard moulding techniques to produce plastic parts. While this method can achieve satisfactory results, it may not always meet the stringent requirements of certain applications.
Here are some characteristics of traditional injection moulding:
Key Features
1. Standardised Processes: Traditional injection moulding employs established techniques that are well understood within the industry. This includes using standard mould designs and conventional materials.
2. Cost-Effectiveness: For large-scale production, traditional injection moulding can be economically viable. The initial setup costs for moulds can be high, but the per-unit cost decreases significantly with larger production runs.
3. Flexibility: While traditional moulding may not allow for extreme precision, it can adapt to various part designs and materials, making it suitable for a wide range of applications.
Limitations
1. Dimensional Accuracy: Traditional injection moulding can struggle with achieving tight tolerances and maintaining consistency across large production runs. Variations in temperature, material flow, and other factors can lead to discrepancies in the final product.
2. Longer Cycle Times: The cooling time and overall cycle time for traditional injection moulding can be longer, especially when producing more complex shapes.
3. Material Constraints: Traditional moulding may have limitations on the types of materials that can be effectively used, impacting the properties of the final product.
Precision Injection Moulding: A Closer Look
In contrast, precision injection moulding is specifically designed to produce high-quality components with exacting tolerances and consistency. This method is particularly advantageous in industries where precision is paramount, such as aerospace, medical devices, and high-tech manufacturing.
Key Features
1. High Tolerance And Accuracy: Precision injection moulding focuses on achieving tight tolerances, often as precise as ±0.01 mm. This level of accuracy is critical in industries where even minor discrepancies can lead to significant issues.
2. Advanced Technology: This method often utilises advanced technology, including computer-aided design (CAD) and computer-aided manufacturing (CAM), to create intricate moulds and optimise the injection process. This leads to enhanced control over the parameters involved in moulding.
3. Shorter Cycle Times: Precision injection moulding typically offers reduced cycle times compared to traditional methods. Advanced cooling techniques and optimised injection processes help achieve quicker production rates.
Benefits
1. Enhanced Product Quality: With tighter tolerances and improved consistency, products manufactured through precision injection moulding exhibit fewer defects, leading to higher customer satisfaction.
2. Material Versatility: Precision moulding can accommodate a broader range of advanced materials, including high-performance plastics that require specific properties for demanding applications.
3. Reduced Waste: The accuracy of precision injection moulding means that there is less waste generated during production, making it a more sustainable option.
The Key Differences Between Precision And Traditional Injection Moulding
To highlight the distinctions between these two methods, let's break down the main differences:
1. Dimensional Accuracy
- Precision Injection Moulding: Achieves tight tolerances (±0.01 mm or better), suitable for high-precision applications.
- Traditional Injection Moulding: Generally offers looser tolerances, which can lead to variability in product dimensions.
2. Cycle Times
- Precision Injection Moulding: Features shorter cycle times due to advanced cooling methods and process optimisation.
- Traditional Injection Moulding: Often involves longer cycle times, particularly for complex shapes or larger parts.
3. Cost Consideration
- Precision Injection Moulding: Higher initial costs for mould design and manufacturing, but lower per-unit costs for large runs due to improved efficiency.
- Traditional Injection Moulding: More cost-effective for large volumes but may lead to higher rework costs due to dimensional inaccuracies.
4. Material Compatibility
- Precision Injection Moulding: Can use advanced materials with specific properties needed for demanding applications.
- Traditional Injection Moulding: Typically limited to standard materials, which may not meet the requirements of all applications.
Which Method Should You Choose?
The choice between precision injection moulding and traditional injection moulding largely depends on your specific project requirements:
Choose Precision Injection Moulding If:
- You need parts with high precision and tight tolerances.
- Your application requires advanced materials with specific properties.
- Product quality and consistency are paramount.
- You are looking for a long-term production solution with lower waste and improved efficiency.
Choose Traditional Injection Moulding If:
- You are producing large quantities of simpler components where precision is not critical.
- You have budget constraints and need a more economical solution for high-volume production.
- Your application allows for flexibility in design and material selection.
Making The Right Choice For Your Business
Understanding the differences between precision injection moulding and traditional injection moulding is essential for manufacturers looking to optimise their production processes. Each method has its strengths and limitations, and the best choice will depend on your specific needs, the complexity of your products, and the importance of precision in your applications.
By carefully evaluating these factors and considering the long-term implications of your manufacturing decisions, you can select the most suitable injection moulding method for your business. Whether you opt for precision injection moulding or traditional injection moulding, both approaches play a vital role in the ever-evolving landscape of modern manufacturing.