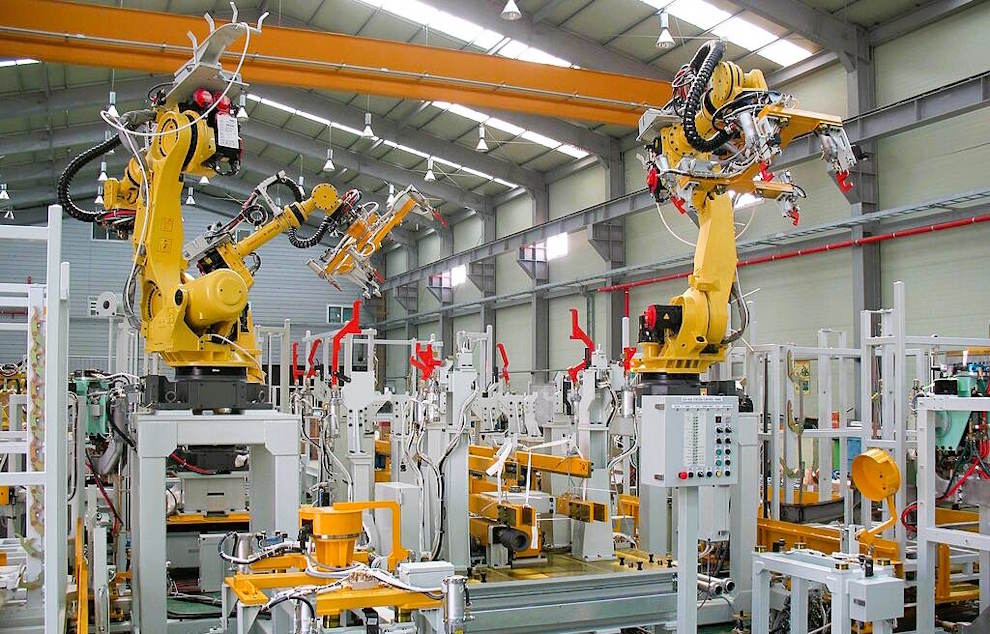
Operational efficiency is the cornerstone of success in the manufacturing sector. With increasing global competition, shrinking profit margins, and rising customer expectations, manufacturers must find ways to optimise their processes without sacrificing quality.
ISO 9001, the internationally recognised standard for quality management systems (QMS), provides a structured framework that enables organisations to achieve these goals. By implementing ISO 9001, manufacturers can streamline their operations, reduce waste, and ultimately enhance their bottom line.
The Basics Of ISO 9001
At its core, ISO 9001 focuses on establishing a quality management system that ensures consistent product quality while meeting customer and regulatory requirements.
The standard is built on principles such as customer focus, leadership involvement, employee engagement, process improvement, and evidence-based decision-making. While its primary aim is to guarantee quality, its impact on operational efficiency is equally transformative.
Streamlining Processes Through Standardisation
One of the fundamental ways ISO 9001 enhances efficiency is by encouraging manufacturers to document, standardise, and optimise their processes.
Standardisation ensures that every task is carried out consistently, reducing variability and the risk of errors. For example, a manufacturer of automotive parts might use ISO 9001 guidelines to develop detailed work instructions for machining components. These instructions ensure that operators follow the same steps every time, leading to predictable outcomes and fewer defects.
Moreover, standardised processes make it easier to train new employees, reducing the learning curve and increasing productivity. When everyone follows the same procedures, the organisation can operate more smoothly and with fewer disruptions.
Identifying And Eliminating Waste
ISO 9001 requires organisations to monitor and measure their processes to identify inefficiencies and areas for improvement.
By analysing key performance indicators (KPIs), manufacturers can pinpoint bottlenecks, redundant steps, or activities that do not add value. This aligns closely with lean manufacturing principles, which aim to eliminate waste in all forms—whether it’s excess inventory, overproduction, or unnecessary motion.
For instance, a company producing electronic components might discover through ISO 9001’s process monitoring that certain quality checks are being performed multiple times unnecessarily. By streamlining these inspections, they can save time and resources while maintaining the same level of quality.
Encouraging A Culture Of Continuous Improvement
Continuous improvement is a central tenet of ISO 9001. The standard’s Plan-Do-Check-Act (PDCA) cycle encourages organisations to regularly review their processes, identify areas for enhancement, and implement changes. This iterative approach ensures that improvements are not one-off events but an ongoing part of the organisation’s culture.
Take, for example, a furniture manufacturer that uses ISO 9001 to track production downtime. By analysing data over time, they may identify recurring equipment failures as a major source of inefficiency. Acting on this insight, they could invest in preventive maintenance programs or upgrade their machinery.
These actions not only improve efficiency but also reduce the likelihood of costly disruptions in the future.
Enhancing Communication And Collaboration
ISO 9001 places a strong emphasis on communication and collaboration within an organisation. Clear communication channels ensure that everyone understands their roles, responsibilities, and the organisation’s quality objectives. This reduces misunderstandings, duplication of efforts, and wasted time.
For example, a manufacturer of medical devices might use ISO 9001 to establish cross-functional teams that bring together design, production, and quality assurance departments. By fostering collaboration, these teams can identify potential design flaws early in the process, avoiding costly rework and delays further down the line.
Data-Driven Decision-Making
ISO 9001’s focus on evidence-based decision-making helps manufacturers make informed choices that improve efficiency. By collecting and analysing data, organisations can gain valuable insights into their operations and identify trends that might otherwise go unnoticed.
Consider a food and beverage manufacturer that uses ISO 9001 to track production yields. If the data reveals a consistent drop in output during certain shifts, management can investigate the root cause—perhaps inadequate staffing or outdated equipment—and take corrective action.
This data-driven approach ensures that resources are allocated effectively and that improvements are based on facts rather than assumptions.
Integrating Technology For Greater Efficiency
In today’s digital age, ISO 9001 can be seamlessly integrated with advanced manufacturing technologies to further enhance efficiency.
For instance, organisations can use Enterprise Resource Planning (ERP) systems to automate data collection and analysis, ensuring real-time visibility into production processes. Similarly, predictive analytics tools can help identify potential issues before they escalate, enabling proactive decision-making.
A manufacturer of consumer electronics might integrate ISO 9001’s QMS with Internet of Things (IoT) sensors on their production lines. These sensors can monitor equipment performance and send alerts when maintenance is needed, reducing downtime and maximising productivity.
The Tangible Benefits Of ISO 9001
The operational efficiencies gained through ISO 9001 implementation translate into tangible benefits for manufacturers. These include:
- Cost Savings: Reduced waste, fewer defects, and streamlined processes lower operating costs.
- Increased Productivity: Standardised procedures and continuous improvement initiatives lead to smoother operations.
- Improved Customer Satisfaction: Consistently high-quality products enhance the organisation’s reputation and strengthen customer loyalty.
- Competitive Advantage: Efficient operations enable manufacturers to respond more quickly to market demands and stay ahead of competitors.
Overcoming Implementation Challenges
While the benefits of ISO 9001 are clear, implementing the standard is not without challenges.
Some organisations may resist change or view the certification process as overly bureaucratic. However, these hurdles can be overcome with strong leadership, employee involvement, and a clear understanding of the long-term advantages.
Investing in training and engaging employees at all levels is critical. When workers understand how ISO 9001 benefits them—whether through improved workflows or a safer work environment—they are more likely to embrace the changes.
Setting A Superb Standard
ISO 9001 is much more than a quality management standard; it is a powerful tool for driving operational efficiency in manufacturing.
By standardising processes, eliminating waste, fostering continuous improvement, and leveraging data-driven decision-making, manufacturers can achieve significant gains in productivity and profitability. In a competitive and ever-evolving industry, those who embrace ISO 9001 are better positioned to thrive and deliver value to their customers.
Therefore, for manufacturers looking to optimise their operations, ISO 9001 is not just an option—it’s a necessity.