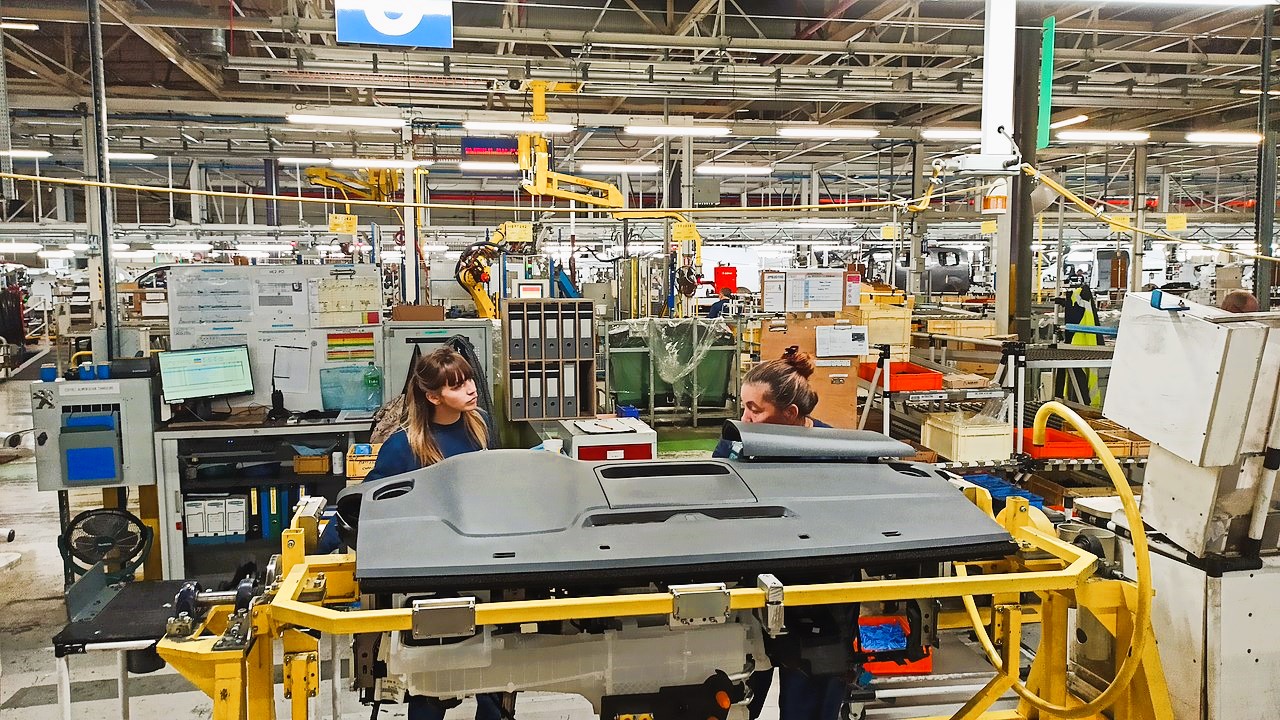
Plastic injection moulding is one of the most widely used manufacturing processes across industries, and its impact on the automotive sector is particularly significant.
The production of modern vehicles relies heavily on this technique, which allows manufacturers to create a vast range of parts that are both durable and lightweight. From dashboards and bumpers to intricate interior components, plastic injection moulding has revolutionised the automotive manufacturing process, offering benefits that were previously unattainable with traditional materials like metal.
In this article, we will explore how plastic injection moulding plays a vital role in shaping the modern automotive industry, highlighting its benefits, applications, and innovations that continue to push the boundaries of vehicle design and production.
What Is Plastic Injection Moulding?
Before diving into its automotive applications, it's essential to understand what plastic injection moulding is. This process involves injecting molten plastic into a mould cavity, which is shaped like the desired part. The plastic is then cooled and solidified, after which the mould is opened, and the part is ejected. This process can be repeated with high precision and at incredible speeds, making it ideal for large-scale manufacturing.
The plastic materials used in injection moulding can vary depending on the requirements of the part. Commonly used materials include polycarbonate (PC), polypropylene (PP), acrylonitrile butadiene styrene (ABS), and nylon (PA), among others. These plastics offer unique properties such as flexibility, strength, durability, and resistance to heat and chemicals, which make them suitable for use in automobiles.
The Role Of Plastic Injection Moulding In Automotive Manufacturing
The automotive industry is a prime example of how plastic injection moulding has been integrated into modern manufacturing processes. Vehicles today contain a wide array of plastic components that enhance both their functionality and aesthetics. Here's how injection moulding is reshaping the industry:
1. Weight Reduction And Fuel Efficiency
One of the most significant advantages of using plastic injection moulding in automotive manufacturing is the reduction of vehicle weight. Lightweight materials such as plastics are much lighter than traditional metals like steel and aluminium. In a vehicle, even a small reduction in weight can lead to significant improvements in fuel efficiency and lower emissions, which is becoming increasingly important as the industry moves toward greener solutions.
By replacing metal parts with plastic alternatives, manufacturers can reduce the overall weight of the vehicle without compromising its structural integrity. This has become crucial in the era of electric vehicles (EVs) as manufacturers seek ways to extend the range of EVs by making them lighter and more efficient. Plastic components such as bumpers, fenders, and door panels are now commonly moulded using injection techniques to achieve this goal.
2. Cost-Effectiveness And Mass Production
Plastic injection moulding is a cost-effective solution for mass-producing automotive parts. The process allows for the creation of complex shapes and detailed designs with minimal waste. Once the mould is created, the cost per unit is significantly reduced, making it ideal for large-scale production runs.
Additionally, the versatility of injection moulding means that a wide variety of parts can be produced using the same basic process, from large exterior components like bumpers to small, intricate interior features such as switches and vents. This scalability allows automotive manufacturers to produce high-quality parts quickly and efficiently, reducing production times and costs.
3. Durability And Longevity
Plastics used in automotive injection moulding are designed to be highly durable and resistant to wear and tear. Components such as dashboards, consoles, and steering wheel covers are regularly subjected to environmental stressors like heat, UV exposure, and physical impact. Plastics like ABS and polypropylene are chosen for their ability to withstand these conditions while maintaining their appearance and functionality over time.
Moreover, plastic parts are less susceptible to rust and corrosion compared to metal components, particularly in areas exposed to moisture, such as underbody shields and wheel arches. This makes plastic injection moulding a practical choice for creating long-lasting parts that require minimal maintenance, further contributing to the overall cost savings for manufacturers and consumers.
4. Design Flexibility And Aesthetic Appeal
One of the most exciting advantages of plastic injection moulding in the automotive sector is the design flexibility it offers. Plastics can be moulded into complex shapes and customised to meet specific design requirements. This allows automotive manufacturers to innovate and experiment with unique, modern vehicle designs.
For example, interior components such as dashboards, door panels, and centre consoles can be moulded with intricate detailing, adding aesthetic appeal and enhancing the driver’s and passengers' experience. The ability to integrate various textures, colours, and finishes during the injection moulding process means that manufacturers can create visually striking parts without the need for additional finishing processes.
Moreover, plastic injection moulding allows for the integration of functional elements such as clips, brackets, and fasteners directly into the part, reducing the need for assembly and improving overall manufacturing efficiency.
5. Sustainability And Recycling
As the automotive industry faces growing pressure to adopt sustainable practices, plastic injection moulding offers several eco-friendly benefits. Many of the plastics used in this process are recyclable, allowing for the creation of automotive parts that can be reused or repurposed at the end of their lifecycle. Additionally, advancements in bio-based and recycled plastics are making their way into the industry, further reducing the environmental impact of vehicle manufacturing.
Injection moulding also minimises material waste by using only the necessary amount of plastic in the moulding process. Excess plastic can often be re-ground and reused, contributing to more sustainable manufacturing practices. This aligns with the automotive industry's push toward reducing its carbon footprint and embracing greener alternatives.
Innovations In Plastic Injection Moulding For The Automotive Industry
The automotive sector is continuously evolving, and plastic injection moulding technology is advancing alongside it. Here are a few notable innovations that are shaping the future of automotive manufacturing:
- Hybrid Materials: Some manufacturers are now exploring hybrid materials that combine the strength of metal with the lightweight properties of plastic. These hybrid parts are produced using injection moulding techniques and offer the best of both worlds: the durability of metal and the design flexibility of plastic.
- Overmoulding: Overmoulding is a process where multiple materials are moulded together to create a single part. This technique is particularly useful in automotive manufacturing for producing parts with enhanced functionality, such as integrating soft-touch elements with rigid components, like steering wheels or handles.
- Smart Plastics: Advances in polymer technology have led to the development of smart plastics that can respond to environmental changes, such as temperature or pressure. These materials are being explored for use in automotive applications where self-healing or shape-changing properties could enhance vehicle performance and safety.
A Key Driver In Automotive Manufacturing
Plastic injection moulding has revolutionised the automotive industry by offering a cost-effective, lightweight, and durable solution for producing a wide variety of vehicle components. As the industry continues to evolve, especially with the rise of electric and autonomous vehicles, plastic moulding will remain a crucial part of the manufacturing process, driving innovation and helping brands meet the demand for efficient, sustainable, and aesthetically pleasing cars.
The flexibility and precision of plastic injection moulding ensure that it will continue to shape the future of automotive design and production, offering manufacturers the tools they need to create cutting-edge vehicles that are not only more efficient but also more visually appealing and sustainable.