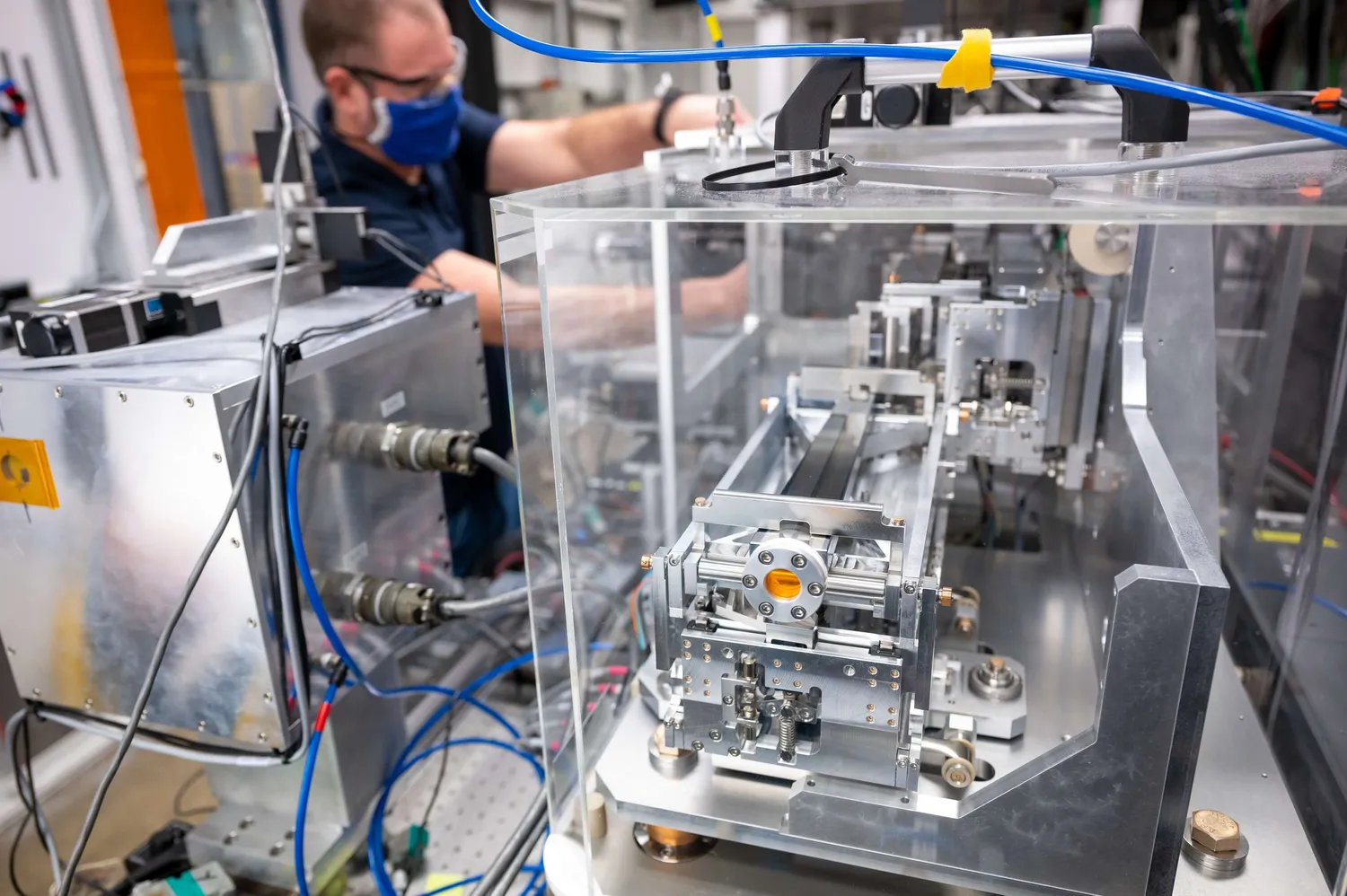
Plastic injection moulding has become essential for manufacturers in many industries. This technique offers many economic advantages, making it a great choice for producing complex and high-volume plastic components.
In this article, we’ll explore some key economic benefits of plastic injection moulding.
Cost Efficiency
A major economic benefit of plastic injection moulding is its cost efficiency. This method allows manufacturers to produce parts more cheaply than with other techniques.
Though the initial investment in mould creation is significant, it’s offset by the lower cost per unit in high-volume production runs. As production volume increases, the cost per piece drops significantly, making it a cost-effective option for large-scale manufacturing.
Scalability And High-Volume Production
Plastic injection moulding excels in high-volume production. Once the moulds are created, the production process can be repeated countless times with consistent quality. This scalability enables manufacturers to fulfil large orders without sacrificing product uniformity.
The capability to produce thousands or even millions of identical parts efficiently reduces overall production costs and boosts profit margins.
Reduction In Labour Costs
Automation is a key feature of plastic injection moulding, reducing the need for extensive manual labour.
Modern injection moulding machines require minimal human intervention, lowering labour costs. This automation not only cuts expenses but also enhances production speed and consistency.
Fewer human errors result in higher quality products and fewer defective units, saving on costs related to waste and rework.
Material Efficiency And Waste Reduction
The plastic injection moulding process is highly efficient in material usage. Moulds are designed to use the exact amount of plastic needed, minimising waste, while excess plastic can often be recycled and reused in the production process.
This efficient use of materials lowers costs and supports sustainable manufacturing practices, which are increasingly important in today’s market.
Economies Of Scale
Plastic injection moulding benefits significantly from economies of scale.
As production volume increases, the average cost per unit decreases, making it more cost-effective for large orders. This principle applies to both direct manufacturing costs and overheads, which are spread over a larger number of units.
These economies of scale make injection moulding particularly attractive for industries requiring mass production, such as automotive, consumer goods, and electronics.
Consistent Quality And Precision
Consistency in product quality is crucial for maintaining brand reputation and customer satisfaction, while high-quality products reduce the likelihood of returns and defects, saving costs associated with customer complaints and product recalls.
Plastic injection moulding ensures that each part produced is nearly identical; this precision is achieved through well-designed moulds and controlled production processes.
Speed Of Production
The speed of plastic injection moulding is another significant economic benefit. The process is much faster compared to methods like machining or 3D printing, especially for large quantities.
This rapid production capability allows manufacturers to meet tight deadlines and respond quickly to market demands. Faster production times also mean shorter lead times and quicker time-to-market for new products.
Design Flexibility And Innovation
Plastic injection moulding offers great flexibility in product design. Complex shapes and intricate details that are difficult or impossible with other methods can be easily achieved.
This flexibility enables manufacturers to innovate and create products tailored to specific customer needs, helping them stand out in the market. Innovative designs can command higher prices, improving overall profitability.
Lower Energy Costs
Advancements in injection moulding technology have led to more energy-efficient machines. These modern machines use less power than older models, resulting in lower energy costs for manufacturers.
Energy-efficient production not only reduces operational costs but also supports environmental sustainability, which can attract eco-conscious consumers.
Versatility In Material Choices
Plastic injection moulding offers versatility in material selection. Manufacturers can choose from a wide range of plastics, each with unique properties to suit different applications.
This versatility allows for cost optimisation by selecting the most appropriate and cost-effective material for each part. Additionally, manufacturers can experiment with new materials to enhance product performance and reduce costs further.
Moulding The Modern World
The economic benefits of plastic injection moulding are clear and compelling. From cost efficiency and scalability to material efficiency and rapid production, this manufacturing process offers numerous advantages that help manufacturers reduce costs and increase profitability.
As technology continues to advance, the benefits of plastic injection moulding will likely grow, solidifying its position as a cornerstone of modern manufacturing.