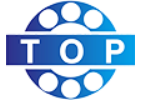
Ball bearings are crucial components in various industries, ensuring smooth and efficient movement in machines and systems. From automotive parts to industrial machinery, these bearings play a key role in reducing friction and enhancing performance. Understanding the manufacturing process and the importance of quality control is essential when choosing a ball bearing supplier. This article will take you through the journey of ball bearing production inside a factory, shedding light on the process and why selecting a reliable ball bearing manufacturing factory is crucial for the durability and reliability of your bearings. Look At Here Now
The Ball Bearing Manufacturing Process
Ball bearings are typically made of steel or ceramic materials, with the manufacturing process involving several precise steps to ensure high-quality products. The process begins with raw materials being carefully selected to meet specific requirements based on the application of the bearings. Once the materials are ready, the ball bearing manufacturing factory begins with the formation of the bearing components.
1. Forging and Machining
The first step in ball bearing production is forging. The raw material, often steel, is heated and then pressed into the desired shape of the bearing rings and balls. After forging, machining processes follow, where the components are finely shaped using lathes and milling machines. This process ensures the components meet the required dimensions and surface finish for optimal performance.
2. Ball Creation and Heat Treatment
After the rings are shaped, the steel balls used in the bearing are also manufactured. These balls are created using a process known as cold heading, which forms the balls into the necessary size and shape. Once the components are formed, they undergo heat treatment to increase hardness and improve wear resistance, ensuring the longevity of the bearings.
3. Assembly
Once all the components are machined and treated, the ball bearings are assembled. The balls are placed between the inner and outer raceways, and the assembly is then checked for accuracy. This step also involves the insertion of a cage or separator, which ensures that the balls remain evenly spaced within the bearing, allowing smooth and efficient operation.
Quality Control in a Ball Bearing Manufacturing Factory
Quality assurance is critical in the ball bearing manufacturing process. Bearings are used in high-precision applications, so ensuring that each bearing meets strict quality standards is essential. A reliable ball bearing manufacturing factory will have several measures in place to ensure the consistency and reliability of their products.
1. Dimensional Accuracy
One of the primary checks in quality control is ensuring that the bearings meet precise dimensional specifications. This includes checking the diameter, roundness, and surface finish of the components. High-precision measurement tools, such as coordinate measuring machines (CMMs), are often used to verify the accuracy of these dimensions.
2. Material Testing
To ensure that the bearings will perform well under different operating conditions, the materials used for manufacturing are carefully tested. The material’s hardness, tensile strength, and resistance to wear are all assessed. The testing ensures that the bearings will perform efficiently and last longer, even under high-speed and heavy-load conditions.
3. Performance Testing
Finally, after assembly, the ball bearings undergo performance testing. These tests simulate the actual operating conditions the bearings will face in the field. Common tests include checking for noise, vibration, and load capacity. This helps to identify any potential issues before the bearings are shipped to customers, ensuring they are ready for reliable use.
The Benefits of Choosing a Reliable Ball Bearing Manufacturing Factory
Choosing the right ball bearing manufacturing factory is crucial for ensuring the performance and reliability of the bearings you use. A trusted factory will deliver consistent quality, meeting your specific needs and the standards of your industry. Here are some benefits of working with a reputable supplier:
1. High-Quality Bearings
A reliable ball bearing manufacturing factory uses advanced technology and strict quality control processes to ensure that their bearings are durable, efficient, and perform at optimal levels. This reduces the risk of premature failure and costly repairs in machinery.
2. Customization Options
Leading manufacturers offer a range of customization options, allowing you to select bearings that fit your specific needs. Whether you need a special size, material, or design, working with an experienced supplier ensures that you can get bearings tailored to your application.
3. Cost-Effectiveness
While it may seem that cheaper bearings are a cost-saving option, poor-quality bearings can lead to higher maintenance costs and premature equipment failure. By choosing a reliable manufacturing factory, you invest in durable bearings that will save you money in the long run by reducing the need for replacements and maintenance.
4. Timely Delivery and Support
A well-established ball bearing manufacturing factory has efficient production and logistics systems in place to ensure timely delivery of orders. Additionally, they provide excellent customer support, helping you with any issues that may arise during the purchasing process or after installation.
The Importance of Selecting the Right Ball Bearing Manufacturing Factory
The ball bearing manufacturing process is intricate and requires precision at every step. By working with a reputable supplier, you can ensure that you are getting high-quality bearings that will perform reliably under various conditions. Quality control, timely delivery, and customization options are just some of the factors that make a ball bearing manufacturing factory stand out.
Investing in high-quality bearings from a trusted factory not only guarantees better performance but also extends the life of your machinery, reduces maintenance costs, and ultimately improves operational efficiency. Whether you're working in automotive, aerospace, or industrial applications, selecting a leading ball bearing manufacturer is key to achieving the best results for your equipment.
Credible Source :https://en.wikipedia.org/wiki/Ball_bearing