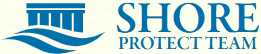
When considering a bulkhead for your property, it's important to understand the bulkhead cost. Bulkheads are essential structures that help prevent soil erosion and protect waterfront properties from water damage. Whether you're constructing a new bulkhead or repairing an existing one, understanding the factors that influence the bulkhead cost is key to budgeting your project effectively. Find Here
What is a Bulkhead?
A bulkhead is a barrier or retaining wall built along the shorelines of rivers, lakes, or oceans. Its purpose is to protect the land from erosion caused by wave action, water flow, or storms. Bulkheads are typically made from a variety of materials, including wood, steel, concrete, or riprap. The choice of material affects both the durability of the structure and the overall bulkhead cost.
Bulkheads are crucial for properties located near water, providing long-term protection and preserving valuable land. However, they can be costly to install or repair, depending on the size, materials, and complexity of the project.
Factors That Influence Bulkhead Cost
Several factors contribute to determining the bulkhead cost for your property. Below are the key elements that influence the price:
1. Material Choice
The type of material used for the bulkhead is one of the primary determinants of the bulkhead cost. Common materials include:
* Wood: Wood is a traditional choice for bulkheads and is relatively affordable. However, it may not last as long as other materials and can require more maintenance.
* Steel: Steel bulkheads are more durable and can withstand harsh weather conditions, but they are typically more expensive.
* Concrete: Concrete bulkheads offer strength and longevity but come at a higher initial cost.
* Riprap: A more natural option, riprap bulkheads use large rocks to create a protective barrier. While it may be less expensive initially, its cost can vary depending on the rocks used and the installation process.
Choosing the right material based on your budget and environmental conditions is critical in estimating the overall bulkhead cost.
2. Length of the Bulkhead
The length of the bulkhead is another key factor in determining the bulkhead cost. A longer bulkhead requires more materials, labor, and time to construct, making it more expensive. For example, if you are protecting a large stretch of shoreline, the cost will increase significantly compared to a smaller, more localized bulkhead.
It's important to accurately measure the length of your shoreline and determine how much of it needs to be protected. This will give you a better estimate of the overall costs associated with your project.
3. Site Conditions
The conditions of the site where the bulkhead will be built can also impact the bulkhead cost. Factors such as soil type, water depth, and accessibility can make the installation process more difficult and costly. For example, if the site is difficult to access with equipment, the labor costs may increase. Similarly, if the soil is unstable, additional measures may be needed to ensure the bulkhead's stability.
If the location requires specialized equipment or labor to install the bulkhead, this can further increase the total project cost.
Average Bulkhead Cost
On average, the bulkhead cost can range from \$30 to \$50 per linear foot, depending on the materials used and site conditions. Here's a breakdown of the general cost estimates for different types of bulkheads:
* Wooden Bulkheads: Typically cost between \$30 and \$40 per linear foot for a standard installation.
* Steel Bulkheads: Steel bulkheads can cost between \$40 and \$60 per linear foot, depending on the thickness and grade of steel used.
* Concrete Bulkheads: These are the most expensive option, ranging from \$50 to \$75 per linear foot for installation.
* Riprap Bulkheads: Riprap bulkheads generally cost between \$30 and \$45 per linear foot, but this can vary based on the type of rock used and the complexity of the project.
While the initial investment in a bulkhead might seem high, it’s important to consider the long-term benefits, such as reduced erosion and increased property value.
How to Plan for Bulkhead Installation
To ensure a successful bulkhead installation, it's important to follow these steps:
1. Assess Your Property's Needs: Determine the length of the shoreline to be protected and assess the site conditions. This will help you choose the right materials and estimate the cost.
2. Choose the Right Contractor: Hire a professional contractor with experience in bulkhead installation. A skilled contractor will ensure that the job is done correctly and efficiently.
3. Get Multiple Quotes: Contact several contractors to get quotes based on your project’s specific requirements. This will help you compare prices and ensure you are getting a fair rate.
4. Consider Long-Term Maintenance Costs: Some bulkhead materials, like wood, require more maintenance over time. Be sure to factor in any ongoing costs for repairs or maintenance when planning your budget.
Why a Bulkhead is Worth the Investment
While the bulkhead cost may seem significant, the benefits far outweigh the initial expense. A well-built bulkhead offers long-term protection against erosion, improves the stability of your property, and can even enhance its aesthetic value. By carefully considering the material, length, and site conditions, you can make a well-informed decision that aligns with your budget and long-term goals.
Investing in a bulkhead is a smart choice for property owners near water. It provides peace of mind knowing that your property is protected from the unpredictable forces of nature.
Important Read :https://en.wikipedia.org/wiki/Retaining_wall