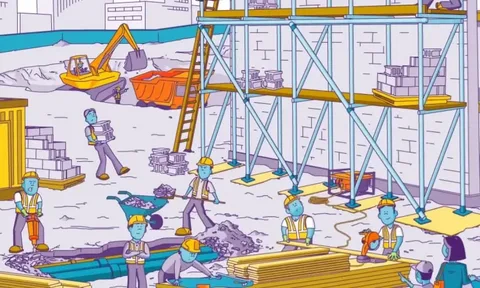
Occupants of the working environment must comply with a certain threshold of safety and health required by the state, monitoring workplace environment risks, policies, and precautionary procedures. It is therefore the responsibility of employers to continuously implement infrastructural and technological changes to ensure a safe working condition for their employees. According to statistics, every year thousands of workers fall victim to workplace hazards, resulting in workplace illnesses and injuries. There are various workplace hazards that are broad in nature and include physical and chemical risks, ergonomic and psychosocial risks. This blog aims to highlight the most prevalent risks to health and safety while offering appropriate and easy measures to manage them.
1. Physical Hazards
Examples:
• Slips, trips, and falls:
• Noise exposure:
• Temperature extremes:
Slips, trips, and falls are classified as physical hazards and are considered the most basic hazards faced by employees in workplaces. Non-slippery surfaces, tidy pathways into buildings, sufficient lighting in and around workplaces, all contribute to preventing accidents. Hearing problems can stem from unchecked noise. Providing thermal regulation clothing can prevent workers from suffering heatstroke or frostbite.
Prevention Tips
• It is advised that everyone monitors and manages their surroundings with frequent checks to improve safety.
• Use matting for thermal insulation of marine vessels and assist with lighting installation.
• Work with personal protective equipment, ear protection, and clothing for thermal regulation as PPE.
• Implement programmes to educate employees on the prevention of physical hazards, such as OSHA training programmes.
2. Chemical Risks
Factors Related
• Working with harmful gases, solvents, and dust particles.
• Working with skin-irritating liquids.
Chemical hazards are encountered in construction, manufacturing, healthcare, and many other sectors. Employees who come into contact with harmful chemicals without proper protective measures may sustain burns or respiratory diseases, including chronic bronchitis.
How to Reduce Chemical Risks Include
• Use adequate PPE such as gloves, face masks, and safety glasses.
• Conduct regular risk assessments.
• Train employees through OSHA online courses to better understand the chemicals involved, including their handling, application, and storage.
3. Physiological Risks
Examples Include
• Non-ideal workstation layout.
• Continuous body movements without proper breaks.
• Excessive load lifting.
Office workers, warehouse employees, and factory workers may be affected by musculoskeletal disorders caused by ergonomic risks. Such disorders rarely turn out to be one-off issues; rather, they tend to become chronic, inevitably reducing a worker's productivity.
How to Lower Those Risks Include
• Provide desks and chairs at the appropriate height, including adjustable options.
• Supply ergonomic tools, including softer tools.
• Offer OSHA outreach online training to prevent improper posture and incorrect lifting techniques.
4. Electrical Risks
The Possible Impacts of Electrical Risks Include
• Always frayed wiring.
• Excessive availability of live connections.
• Operating alongside active electrical sources.
Electrical hazards can cause severe injuries, including disintegration, serious burns, and in more severe cases, even death. These electricity-related risks are common within maintenance and construction tasks.
Prevention Tips:
• Perform scheduled maintenance on electrical systems.
• Provide appropriate warning signs for high-voltage areas.
• Ensure workers obtain OSHA certification online to learn relevant electrical protocols.
5. Psychosocial Hazards
Examples:
• Anxiety in the workplace.
• Workplace bullying or harassment.
• Excessive working hours.
Psychosocial hazards may not be perceived as significant but can be detrimental to people's well-being and productivity. Stressful environments or hostility in interpersonal relations can lead to burnout, anxiety disorders, and depression.
Prevention Tips:
• Create a supportive work environment.
• Provide access to counselling and mental health services.
• Raise awareness of psychosocial hazards among managers, employees, and other staff.
The Role of OSHA in the Workplace
The Occupational Safety and Health Administration (OSHA) notifies workers of their rights and responsibilities concerning health, liability, and hazards in the workplace, and how to manage them effectively. The OSHA certification programme and outreach training programme are designed to equip workers and employers with the fundamentals needed to avoid exposure to workplace hazards. Such training is relevant to construction, hospitality, healthcare, and other occupational segments.
Moreover, OSHA courses are provided online so that workers can learn at their own pace and from the comfort of their own homes. Therefore, it is by taking an OSHA programme that workers are guaranteed improved safety consciousness and contribute towards a safer workplace environment.
Conclusion
Workplace hazards are unavoidable; however, they can be well managed through strategies and training. First of all, workplace safety should become the absolute priority for employers, by addressing issues such as risk assessment, providing personal protective equipment (PPE), and ensuring adequate training (such as OSHA certification online). Dealing with the health and safety of employees in a responsible manner positively affects their attitude and performance too. Thus, the realisation of the various risks and managing them can lead to much safer conditions, which ultimately can further increase the productivity of organisations.